Manutenção eficaz, produção eficiente
As falhas estão presentes na vida de todos nós e, embora, representem grandes perdas para a empresa, há quem se conforma em conviver com elas
Publicado em 2 de abril de 2021 | 10:00
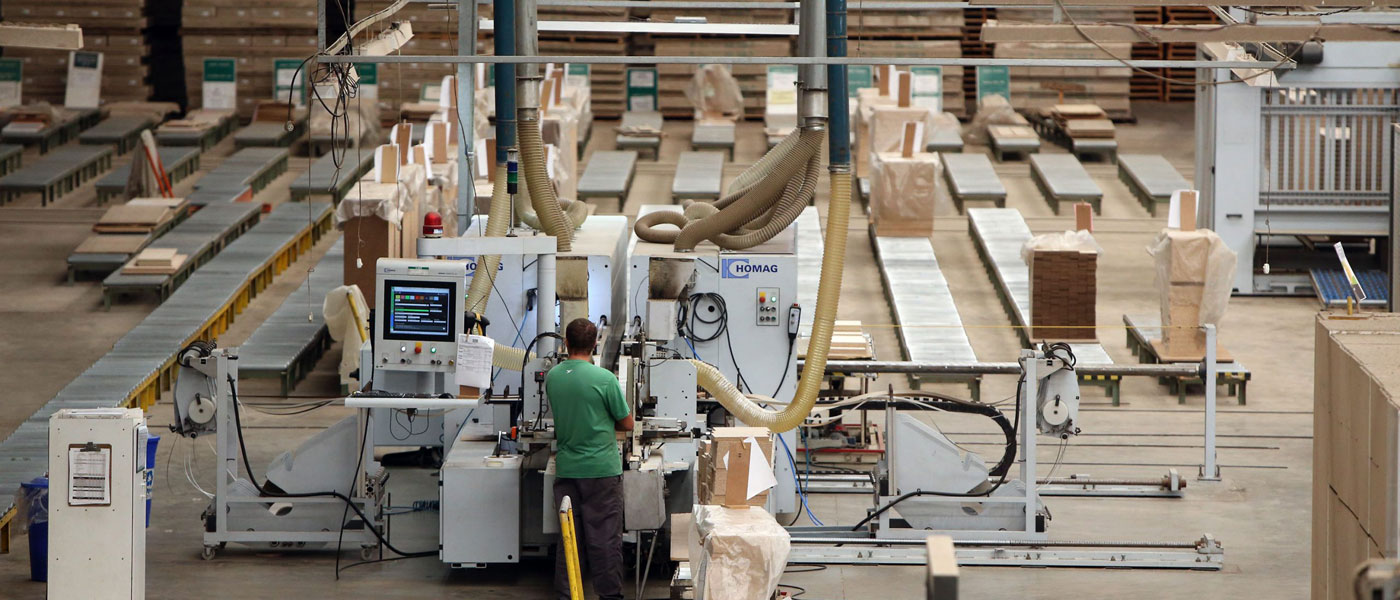
As falhas estão presentes na vida de todos nós e, embora, representem grandes perdas para a empresa, há quem se conforma em conviver com elas. Não é difícil ouvirmos comentários do tipo: “Não temos muito o que fazer, sempre ocorrerão falhas, querendo ou não”.
Esse tipo de pensamento prevaleceu nos cenários fabris até o período da Segunda Guerra Mundial. Por consequência disso, as equipes de manutenção se restringiam somente a reparar falhas para devolverem os equipamentos o mais breve possível dentro de suas funções originais e, vamos ser francos, ainda hoje é possível encontrar um bom número de empresas que mantém essa prática se valendo da máxima da “produção a qualquer custo!”.
Agir somente após a falha não é algo totalmente errado, isso irá depender do impacto que uma possível falha inesperada causaria na produção. Equipamentos em duplicidade, de pouca complexidade estrutural e baixa criticidade em relação ao processo, como furadeiras de coluna e serras de fita, são exemplos que se encaixam nesta situação.
Criando contramedidas
Em 1951, nos Estados Unidos, a necessidade de se obter maior eficiência dos equipamentos fez surgir a Manutenção Preventiva (ações baseadas no tempo ou uso). Após isso, várias outras modalidades foram surgindo, não mais para somente conservar os equipamentos, como também, proporcionar maior eficiência, qualidade, menos acidentes, confiabilidade, dentre outros benefícios.
Atualmente temos um leque considerável de modalidades. Suas definições podem variar dependendo da literatura, mas, as mais conhecidas são: Corretiva, Preventiva, Preditiva, Detectiva, Manutenção por melhoria, Prevenção contra Manutenção e Manutenção Autônoma.
Diante desta grande variedade, cabe ao gestor de manutenção definir criteriosamente qual ou quais serão aplicadas em cada equipamento, suas referências para isso serão: a criticidade do equipamento em relação ao processo (classificação A, B, C), recomendações do fabricante (principalmente para equipamentos em garantia) e seu histórico de falhas. Após isso, a área de Planejamento e Controle de Manutenção (PCM) elabora um Plano de Manutenção para cada equipamento, relacionando todas as atividades e suas respectivas periodicidades.
Uma vez colocado em prática, ao passar do tempo, possivelmente este plano sofrerá algumas revisões, geralmente para incluir ações de contenção de novas falhas que surgiram no período.
Não posso deixar de comentar que, esta prática de analisar as causas das novas falhas e alterar o plano de manutenção, infelizmente, não é muito frequente nas empresas que conheço. Geralmente o que vemos são planos desatualizados (e por consequência, ineficazes) sendo cumpridos religiosamente pelas equipes de manutenção e, de outro lado, ocorrências frequentes de falhas sem nenhuma ação prevista no Plano de Manutenção para preveni-las. Ou seja, quando isso acontece, acabamos tendo perdas com as paradas e desperdício de recursos com preventivas ineficazes.
Manter ou consertar
Com as atividades de manutenção bem executadas será possível acabar com aquela correria já conhecida das equipes de manutenção para ‘apagar incêndios’. Afinal de contas, se a missão do setor de manutenção é de “manter as condições de operação dos equipamentos”, no mínimo, o que podemos esperar é que a ocorrência de uma falha seja uma exceção e não a regra. Costumo dizer que a falha deve ser considerada o “retrabalho da manutenção”.
Como diz Harilaus Xenos, consultor especializado nesse assunto, em seu livro, “Gerenciando a Manutenção Produtiva”, as atividades relacionadas com o tratamento de falhas não devem ser a maior demanda do departamento de manutenção. Suas atividades devem voltar-se a ações que reduzam os custos e aumentem a produtividade operacional, pois, tratar de falhas, somente é um bom negócio para empresas de assistência técnica. Para quem depende de seus equipamentos, as falhas são um desastre!
Esta citação reforça que a máxima citada anteriormente, de que: “as falhas ocorrem independentemente de nossa vontade” não é uma verdade absoluta. Com um acompanhamento sistemático e análises de causas das falhas, é possível minimizar significativamente as paradas e garantir uma maior eficiência dos equipamentos.
Dá para sermos mais exigentes?
Do outro lado do mundo, os japoneses também buscaram formas de garantir a maior eficiência possível de seus equipamentos e, neste contexto, a Toyota entra em cena provando que é possível sermos ainda mais exigentes a ponto de almejarmos a “Falha Zero”, para isso, uma das condições é mudarmos de paradigma sobre esse assunto.
Na abordagem oriental, se toda falha é consequência de uma ou várias causas, por que não as eliminamos antes de causarem o problema? Sabemos que no método convencional, os planos de manutenção já visam eliminar todas estas causas, porém, ainda existem as pequenas anormalidades que surgem no equipamento, as “Anomalias” ou “Falhas Latentes”, que, por serem aparentemente insignificantes, muitas vezes são desprezadas, com o passar do tempo, acabam se agravando e interferindo no funcionamento do equipamento. Alguns exemplos para ilustrar as falhas latentes são: sujeiras, operações incorretas, desgastes, folgas, trincas, vazamentos, etc.
Pensando assim, se tivermos um Plano de Manutenção eficaz e formos exigentes na eliminação das anomalias, por que não vislumbrarmos a “Falha Zero”? E é com esse pensamento que, em 1971 a Toyota implantou o TPM (Manutenção Produtiva Total) e nele, o Pilar da Manutenção Autônoma. Neste pilar, um dos principais focos é desenvolver nos operadores o senso de propriedade de seus equipamentos a ponto de, em forte parceria com a equipe de manutenção, criarem para eles próprios rigorosos planos de limpeza, de lubrificação e de inspeção para identificarem (e eliminarem) toda anomalia que venha surgir em seus equipamentos antes de se tornarem falhas.
Como podemos ver, não nos faltam opções para mantermos uma eficiência satisfatória de nossos equipamentos. A intensidade dos esforços e investimentos em manutenção dependerão da política que a empresa deverá adotar, colocando na balança os riscos e perdas provocados por uma falha em um equipamento e os investimentos em manutenção necessários para evitá-la.
O conteúdo dos textos das colunas do Portal são de inteira responsabilidade dos seus autores originais